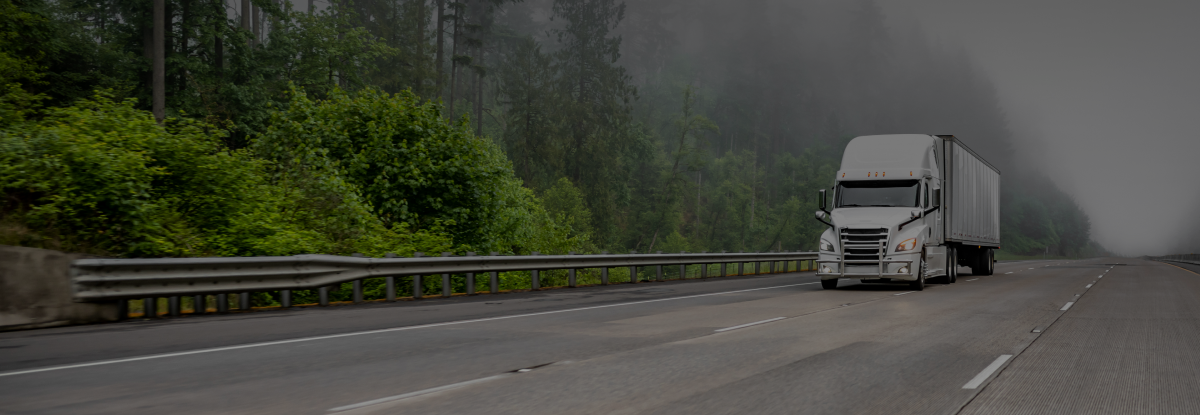
LTL FREIGHT SHIPPING QUOTES
Find the best LTL freight shipping rates from the nation’s top carriers
Get Freight Shipping Quotes5/5
Jim
"We have been working with uShip since 2013 and have always been satisfied with the results."
5/5
Liz
"It was relatively easy to find a shipper and payment was pretty seamless."
5/5
Nate
"My shipper was great! On time both for pick up and drop off would highly recommend."
5/5
Brian
"I can find that hard to deliver item a dependable driver and research their past feedbacks on the platform."
5/5
Jason
“My truck was delivered in pristine condition, and I easily released payment to shipper via uShip's website and that was it! So easy.”
5/5
Jaime
“In every interaction with the team members they have gone above and beyond to ensure I was satisfied with the results.”
5/5
Rebecca
"Our boat arrived in perfect condition."
5/5
Jonathan
"Have used uShip twice to ship a motorcycle purchased out of state. The entire experience has been top notch each time."
5/5
Sheleigh
"Super easy and quick! Very pleased! I will certainly use this platform again."
5/5
Stephen
"uShip provides a service that is unlike anyone else on the planet and I am thankful for it!"
5/5
Alaina
"Wonderful service!!!!! Felt safe and comfortable with how they do payments too! Shipment went better and quicker than expected!!"
5/5
Tony
"The delivery went without a hitch and I cannot say enough good things about the shipper!"
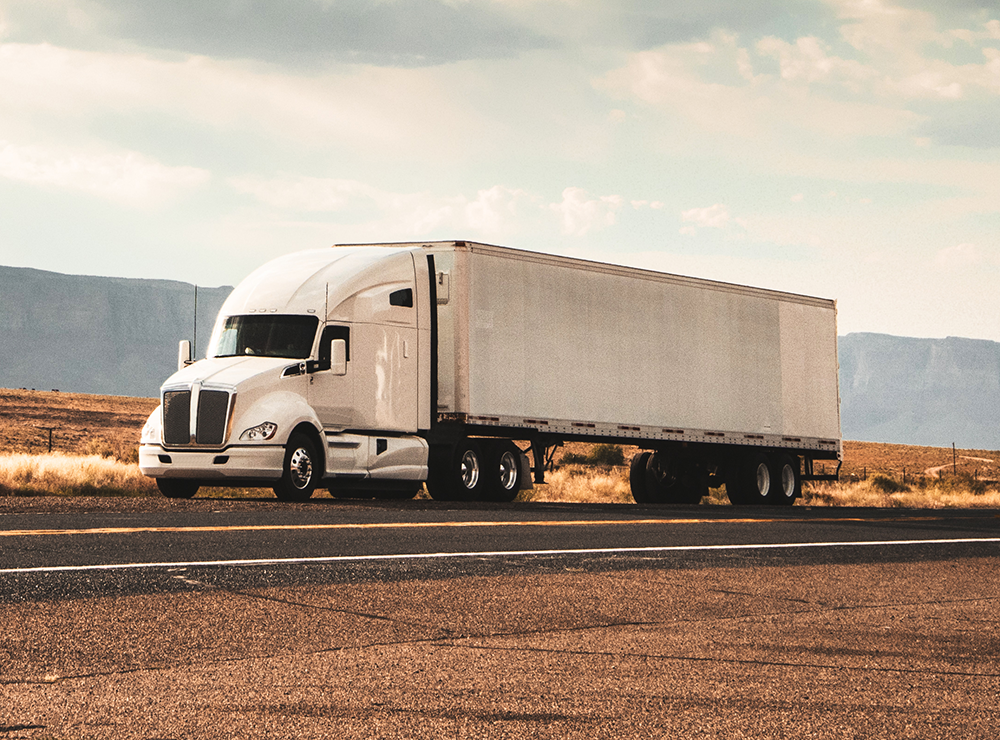
What is LTL Freight Shipping?
LTL shipping, short for less-than-truckload, is the perfect choice for small freight and goods that weigh between 150 and 15,000 pounds. Since this freight does not require a full truckload, you only pay for the space your cargo occupies. With LTL shipping, multiple shipments are consolidated into one, making it an affordable option for moving freight.
Bottom line: Opt for LTL shipping for cost-effective freight solutions and find the best LTL freight quotes with uShip.
What is LTL Freight?
LTL freight can include various items, from car parts and machinery to furniture and appliances, but is ultimately defined as anything shipped in crates or on pallets. Uniform and stackable items like bricks are usually palletized, while delicate and irregular-shaped items, like furniture, are often crated.
Modern freight trailers, typically 8' to 8.5' wide and 40' to 53' long, allow LTL carriers to optimize loads efficiently. This not only maximizes their profits but also leads to cost-effective solutions for you, as the more efficiently they stack freight, the better the LTL shipping rates they can offer. Choose LTL freight for cost-efficient and secure shipping of your goods, and find the best LTL freight quotes on uShip.
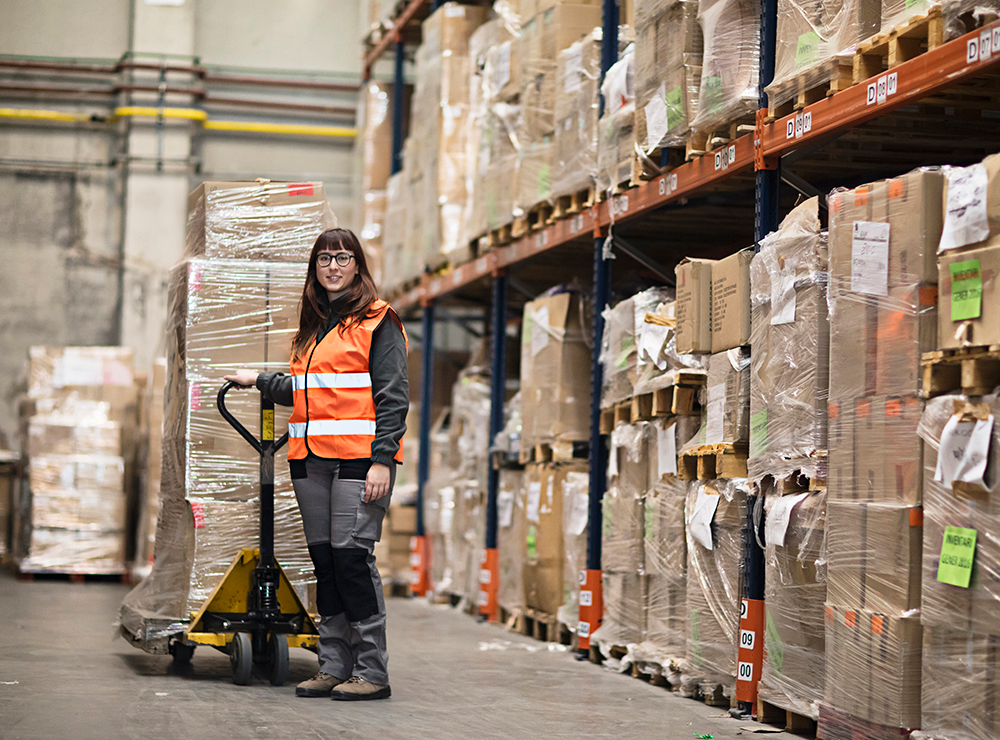
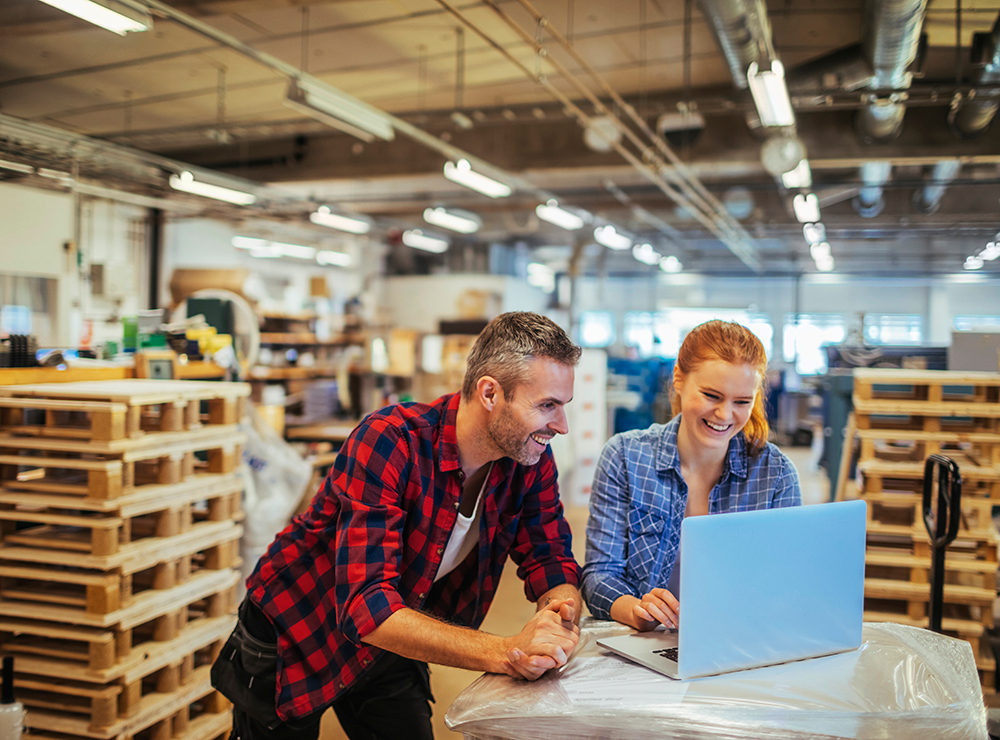
What is an LTL Freight Shipping Rate?
A less-than-truckload shipping rate is an estimate or price provided by a carrier to transport a partial load of goods. This rate is based on factors like weight, dimensions, shipping distance, origin, and destination. LTL freight quotes allow freight shippers to budget for LTL shipping costs and make informed decisions about their logistics needs.
LTL FREIGHT QUOTES FROM USHIP
Streamline Your Business Shipping with uShip's LTL Freight Quotes
Regardless of the size of your business, finding affordable LTL freight rates can be a daunting task. Save time and effort by using uShip's freight shipping marketplace. Our user-friendly platform empowers you to effortlessly compare LTL freight rates from numerous carriers in just a few clicks.
uShip is dedicated to matching business shippers with the right LTL carriers. Our tech-driven interface simplifies the process, making it easy to find budget-friendly LTL carriers for your unique shipping needs. Take the hassle out of shipping and compare LTL freight prices with uShip today.
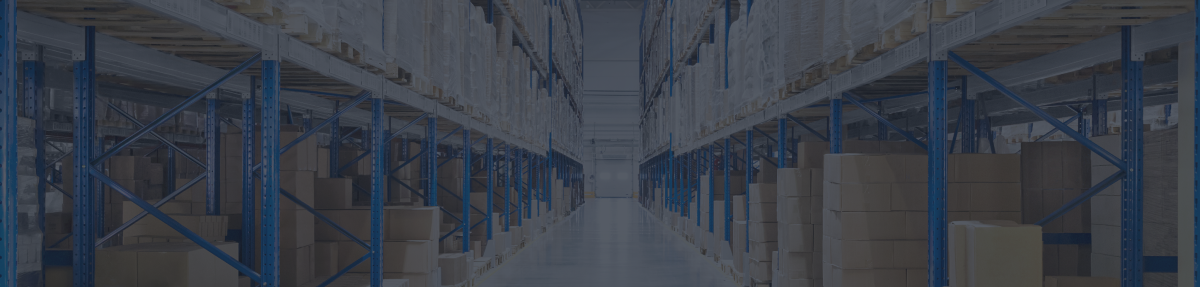
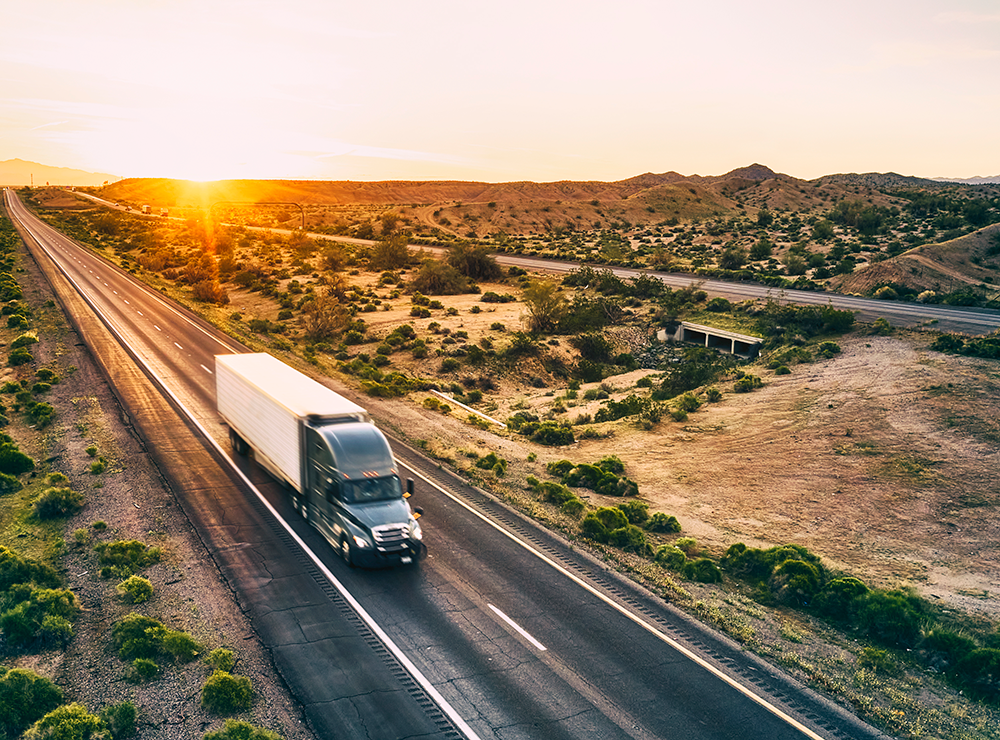
HOW LTL SHIPPING WORKS
Leveraging LTL Shipping for Efficient LTL Shipments and Competitive LTL Rates
- After scheduling your LTL shipment, your carrier collects your cargo at your business location within a specified timeframe.
- Your freight travels to the carrier's local terminal, where it's unloaded and loaded onto another trailer for its journey to the final destination terminal.
- Upon arrival at the destination terminal, the cargo is transferred to a smaller truck for the last-mile delivery to your desired address.
- Remember that any driver-related delays may still incur transport costs, making proactive scheduling a wise choice to ensure smooth LTL shipments and low LTL shipping rates.
WHEN TO USE LESS THAN TRUCKLOAD SERVICES
In general, if your cargo is palletized or crated, it's eligible for LTL shipping. Nonetheless, specific carriers may have limitations on the types of goods they handle. If you're uncertain about your shipment, it's advisable to consult your chosen LTL carrier for clarification.
To assess if LTL freight shipping suits your needs, consider the following questions:
- Is my freight within size limits?
- Am I, or an agent, available to load and unload the shipment?
- Can I consolidate and palletize or crate my shipment?
- Am I comfortable sharing trailer space with other freight shipments?
- Do I understand the timeline restrictions of LTL freight?
Additionally, less-than-truckload shipping is an ideal option when a business has a lot of freight that needs to be transported between the same locations quarterly or monthly.
COST TO SHIP LTL FREIGHT
Less than truckload shipping rates estimate can range from $50 to $5,000+ depending on numerous factors, including the type of freight you’re shipping, the dimensions and weight, the distance the freight will travel, and the type of LTL services you require. To see how much it might cost to ship your LTL freight, see our LTL freight cost calculator.
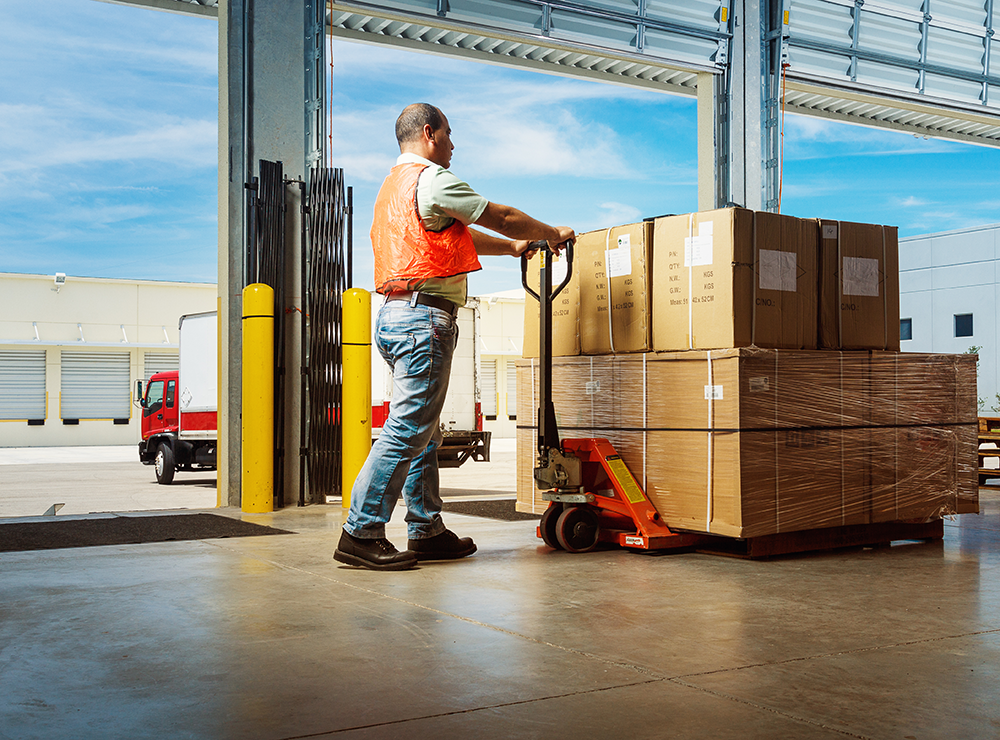

FACTORS DETERMINING LTL SHIPPING RATES
The cost to ship LTL freight can vary depending on many factors, including:
- Distance: Longer distances result in higher costs
- Fuel: Rates are influenced by current fuel prices
- Dimensions: The space your cargo takes up will play a big role
- Weight: Cargo weight is a big determining factor of the final price
- Location Type: Non-dock-to-dock shipments, like to trade shows or military bases, incur higher costs.
Remember, the best LTL freight quotes are notably more cost-effective than shipping bulky items via parcel services.
PROS AND CONS OF LTL DELIVERY
Shipping LTL freight presents a range of advantages and disadvantages. If the drawbacks of less-than-truckload services outweigh the benefits, it's wise to explore alternative shipping methods. For instance, if shipping a delicate piece of furniture that needs extra care, blanket-wrap service may be a more preferable option to consider.
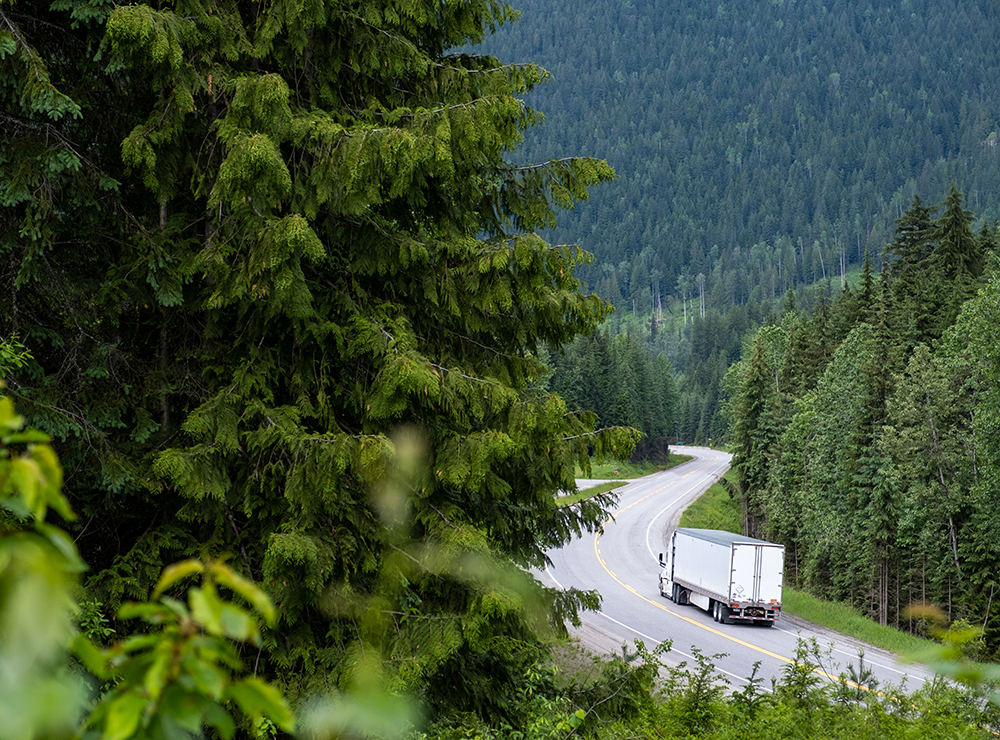
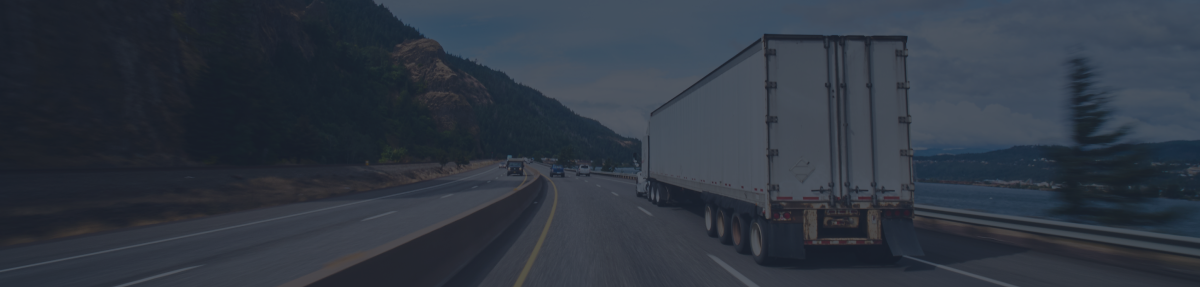
PROS OF LTL DELIVERY
Cost Efficiency:
LTL stands out for its cost-effective pricing structure. By sharing trailer space with other businesses, you pay only for the space your freight occupies.
Eco-Friendly:
LTL freight aligns with the growing emphasis on sustainable business practices. By reducing emissions, it's a step toward greener shipping.
Risk Mitigation:
Robust packaging, typically involving sturdy pallets and crates, significantly reduces the risks of wear, damage, and loss to individual packages.
Easy Tracking:
Many LTL carriers offer real-time shipment tracking, including updates on stop-offs, pickups, and delivery progress. Additionally, services like uShip provide a free portal to track all your shipments in one place.
Service Options:
Most LTL carriers provide a range of service options, including notifications, inside pickup and delivery, liftgate services, special handling, and more, enhancing your flexibility.
Enhanced Safety:
LTL's requirement for durable packaging on pallets or crates substantially lowers the risk of damage during transit.
CONS OF LTL SHIPPING
- Potential Delays: LTL freight services may encounter delays, particularly if issues arise before your scheduled pickup, which can lead to missed deliveries.
- Security Considerations: While LTL is generally secure, it may not offer the same level of security as full truckload (FTL) shipping, which dedicates an entire truck to your freight.
- Less Predictability: Due to multiple stops and transshipments, LTL shipments may be less predictable regarding delivery times.
- Risk of Damage and Loss: Despite being relatively safe, LTL shipments can still experience damage or complete loss, as they are loaded and unloaded multiple times during their journey.
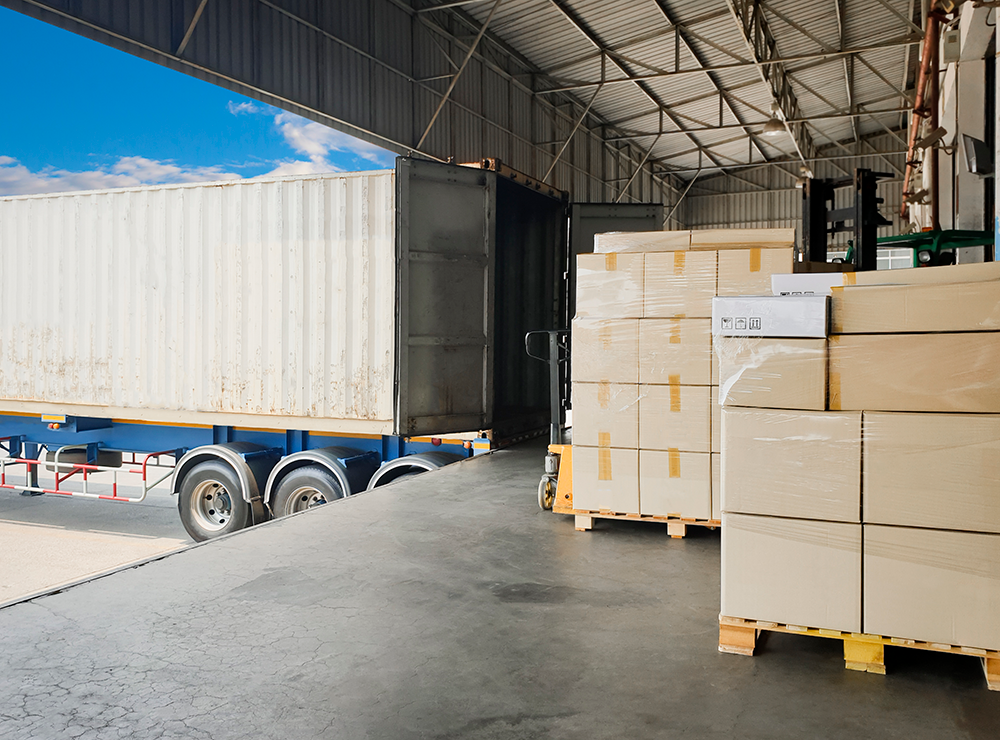
LTL VS FTL SHIPPING
LTL and FTL vary in terms of trailer space usage for individual freight shipments. In the case of less than truckload (LTL), cargo occupies only a portion of the trailer, while full truckload (FTL) completely fills the available space. Moreover, with LTL, the expense is shared with other shippers, reducing costs.
Learn More About the Differences
FREIGHT VS. MOVING SERVICES
Household movers often contemplate the suitability of freight services for their relocation. While services like LTL are traditionally designed for commercial freight, they can also be an option for shipping household goods. However, it's crucial to weigh the advantages and potential drawbacks before deciding.
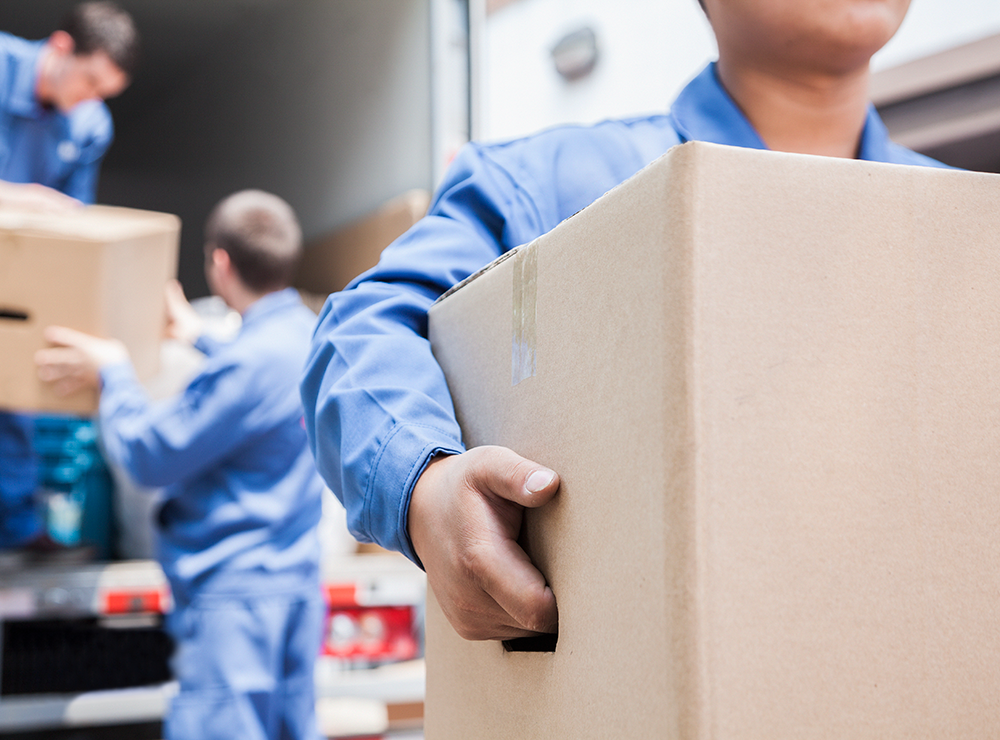
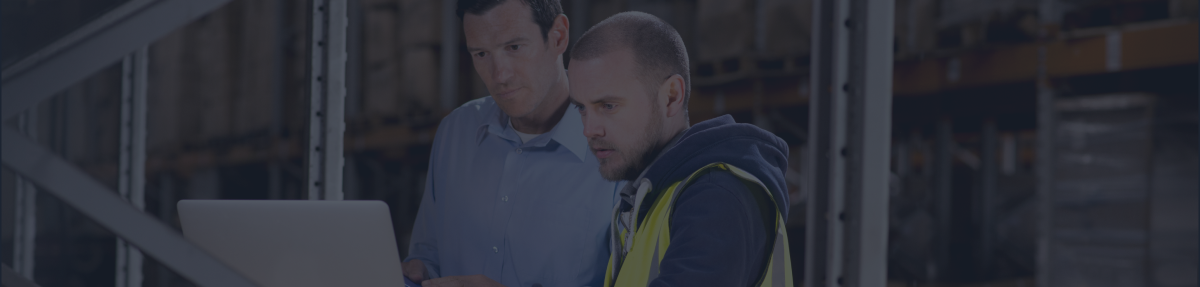
TYPES OF LTL CARRIERS
When it comes to less-than-truckload (LTL) affordable freight shipping, you have the choice of three carrier types: local, regional, and national. Each carrier category offers its unique strengths and weaknesses. To ensure the optimal experience, compare your needs against each carrier type.
LOCAL CARRIERS
Local carriers typically maintain a small truck fleet, catering to areas within a 100-mile radius of major urban centers. They excel in last-mile delivery and providing personalized services. Drawbacks may encompass extended delivery times, relatively higher rates, and limited technological capabilities.
REGIONAL CARRIERS
Regional carriers cover various geographic regions within the United States, boasting a larger fleet than local carriers. This expanded capacity enables them to provide specialized services and expedited transit times. Additionally, regional LTL carriers often collaborate with national carriers to bridge coverage gaps effectively.
NATIONAL LTL CARRIERS
National carriers extend their freight services to all 50 states, though certain carriers may limit operations to the lower 48 states. These carriers operate through an intricate network of national terminals, enabling them to handle pickups and deliveries across the United States. Their advantages encompass competitive pricing, advanced technology, and extensive coverage. uShip’s carrier base is primarily made up of leading national LTL carriers.

LTL SHIPPING SERVICES AND FREIGHT ACCESSORIALS
Less than truckload (LTL) carriers provide a range of versatile service choices, enabling you to tailor your shipment to your specific needs.
Before arranging a pickup with a freight carrier, it's crucial to identify the precise services required. For instance, if your business lacks a loading dock, include this information in your less-than-truckload quote request for an accurate LTL price. Furthermore, if you intend to deliver to a warehouse, like Amazon FBA, seek a carrier experienced in handling such services.
For a comprehensive list of service options for LTL price, consult our guide on services and accessorials.
FREIGHT CLASS
The National Motor Freight Traffic Association (NMFTA) has developed less than LTL truck freight quote classes to standardize pricing. These classes serve as a gauge for carriers to establish the base rate for shipments. Nearly all shippable items are assigned a National Motor Freight Classification (NMFC) code, which, in turn, determines their freight class.
These classes span from 50 (the least expensive) to 500 (the most costly), with density being a key factor. For example, a dense load like a pallet of bricks falls into class 50, while a pallet of lightweight ping pong balls is categorized as class 500.
The advantage of using uShip is that you don't need to navigate the intricacies of NMFC codes, as we calculate freight rates based on density, simplifying the shipping process.
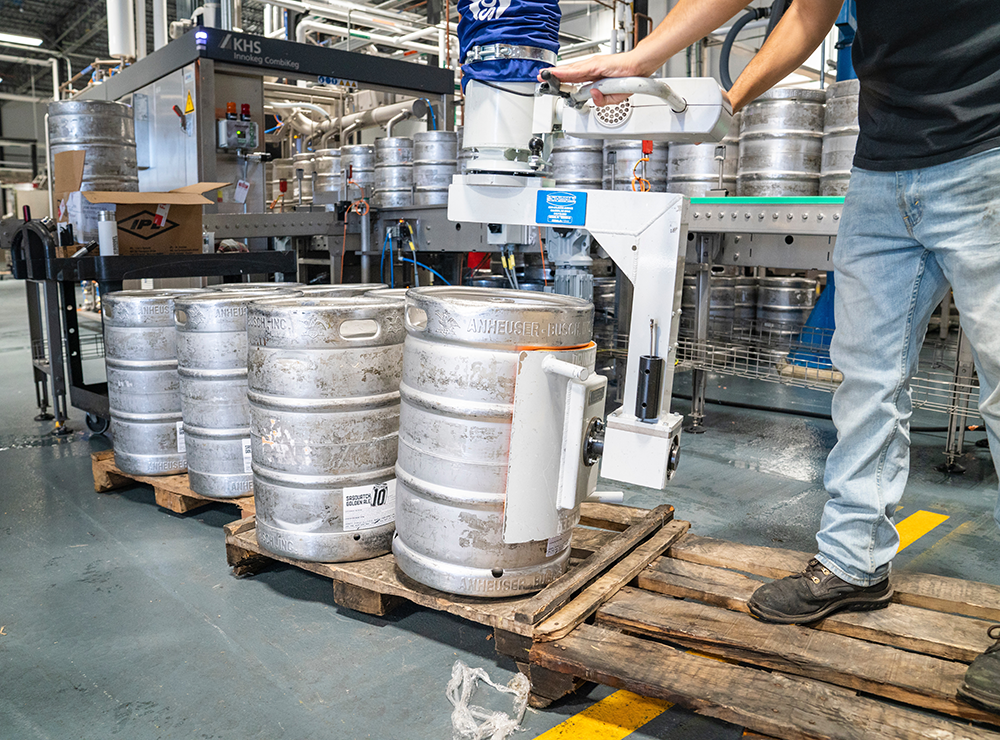
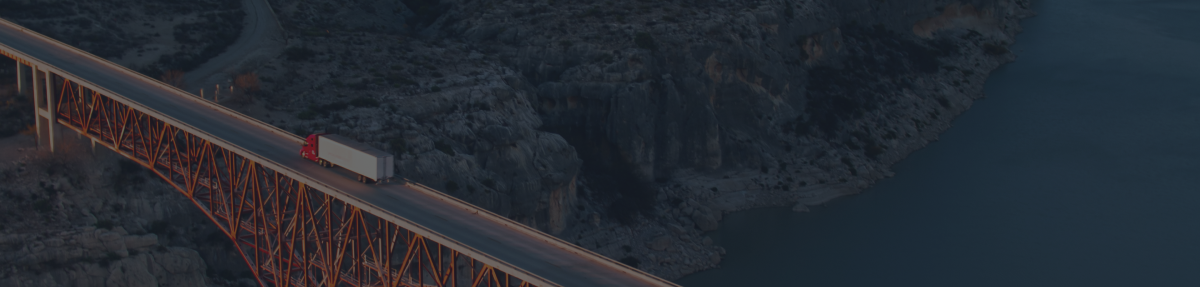
Need LTL FREIGHT SHIPPING QUOTES?
Get Started NowHOW TO SHIP LTL FREIGHT
Properly preparing your LTL freight for transportation reduces the risk of damage and prevents missed pickups. Incorrectly crated, bundled, or palletized freight may lead to your carrier skipping the pickup, requesting corrections, and rescheduling for the following business day.
It's essential to note that each carrier maintains a set of shipment requirements outlined in a "rules tariff," specifying how pallets or crates should be prepared. The primary objective is to safely transport all cargo without shifting. To facilitate this, consider these helpful tips when preparing your LTL cargo for shipping:
- Arrange items with the heaviest at the bottom, avoiding any overhang.
- Utilize straps and shrink wrap to secure the goods in place.
- When packing your LTL shipment, aligning items on the pallet is the best practice, while staggering is acceptable but 33% less stable.
- Affix a label to each pallet, ensuring complete address details, postal codes for the LTL shipper and consignee, and visible phone numbers.
- Accurately weigh and measure your freight to provide precise information to your carrier.
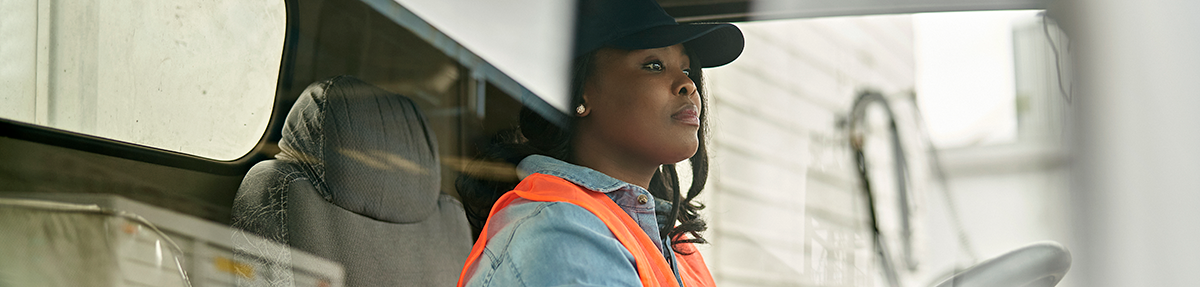
DOCUMENTS NEEDED FOR LTL FREIGHT SHIPPING
For a smooth and delay-free shipment, gathering all the necessary documentation for your freight is vital. Here are common documents you may need:
1. Bill of Lading (BOL): The BOL contains crucial details about your shipment and serves as essential information for both the carrier and the driver.
2. Freight Bill: This document is the invoice encompassing all freight charges linked to the shipment.te dimensions and weight.
3. Proof of Delivery (POD): A POD is utilized upon delivery, with the consignee (the freight recipient) signing it to confirm receipt. Some carriers may use the BOL for confirmation instead of a separate POD.
4. Weight and Inspection Report (W&I): A W&I report is an official carrier document that records your shipment's accurate dimensions and weight.
5. Cargo Claims Form: Complete a claims form only if your cargo is delivered damaged, short, or missing.
HOW USHIP CAN HELP WITH YOUR LTL SHIPMENTS
uShip is an online shipping marketplace that connects business shippers with LTL carriers who have available trailer space. This synergy benefits businesses by offering highly competitive LTL shipping rates, made possible through strong alliances with leading less-than-truckload companies in the industry.
Navigating uShip's marketplace simplifies the search for LTL shipping solutions that align with your freight requirements and budget. To begin, create a detailed listing reflecting your needs. Next, the freight shipping calculator promptly delivers LTL rate estimates. You can accept one of these rates or auction your freight shipment, where transport experts bid for your business, ensuring cost-efficiency and the best LTL freight quotes.
WHY CHOOSE USHIP FOR LTL SHIPPING?
Rebill Protection:
uShip audits your invoice to ensure your carrier made no mistakes on your final bill.
Load Your Own Rates:
If you have your own rates with other carriers, feel free to upload them to your uShip portal. Doing this lets you compare your contract rates against ours, all in one place. Thus, eliminating bouncing around various freight websites for quotes.
Customer-Specific Rates:
If we notice that you are shipping an adequate amount of volume, we can offer account-specific pricing.
Referral Program:
Do you know other businesses needing LTL shipping services? If so, refer them to experience uShip, and you’ll receive shipment credits and other rewards in return.
Protection:
Did you know LTL pickups do not automatically have full coverage protection? uShip fills protection gaps and offers the option to purchase a protection plan for select shipments.
Account Management:
Frequent shippers can enjoy the benefits of having a personal account manager here at uShip.
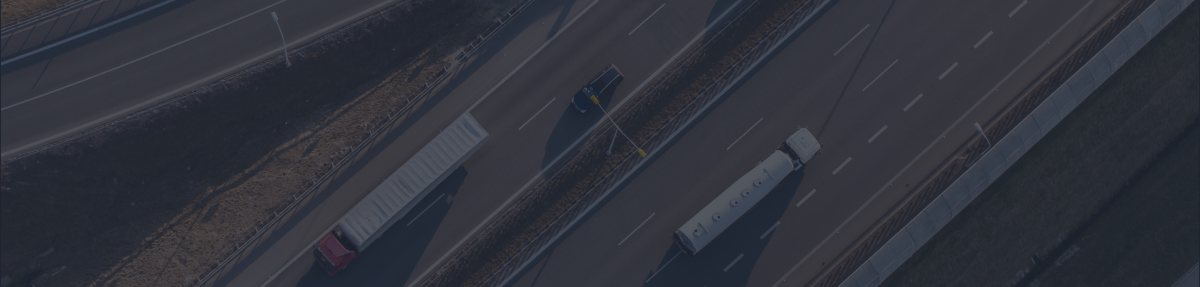